Auditing
MRO Auditing Step 1 in the 6-step improvement process can include:
- MRO Best Practices (a structured questionnaire is used to evaluate best practices in managing spare parts effectively)
- MRO Written Procedures and Guides (the documents required for each phase of an item’s life)
- Master Data Review (short description formats, nouns and modifiers, Mfg. & Vendor P/Ns, Vendor and Mfg. names, review of duplicates)
- Inventory Replenishment Control Parameters (an evaluation of current ROP, OQ, Min-Max, etc)
Ramsoft UK have audited many spares master data-sets and we find most companies do a poor job of cataloguing. This situation results in:
- Excessive duplicates
- Loss of time trying to find the right spare
- Excess downtime
If you are unsure of the status of your spares master data, Ramsoft UK can conduct an initial audit of say bearings, or any other key material group.
Typical findings from our master data audits are:
- Short descriptions have inconsistent formatting
- Qualifiers or Modifiers are not identified
- Vendors’ names included in the short description
- Lack of attribute data in the short description, and inconsistent sequencing
- MPNs have inconsistent formatting
- MPNs fields are a mix of Vendors and MPNs
- 10-15% duplicate line items
- Inconsistent abbreviations used
- Abbreviations are not used when they should be
Multiple suppliers for the similar material
The examples below are from data audits carried out by Ramsoft UK.


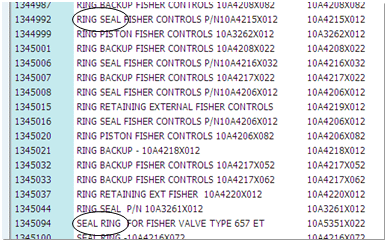
